United States, Germany, and Beyond
Over the past year, we’ve been working closely with a long-term customer to help address many challenges that have impeded their ability to establish and strengthen their position within the United States.
Our customer, an industrial gas supplier with a global footprint, grappled with many intricate issues while constructing new plants and modernizing existing ones across their organization. The challenge was daunting. The need to synchronize the efforts of the engineering and design team at the company’s office in Germany with the production teams in the United States was hindered by time zone disparities and language barriers. Moreover, differences in European and American industrial engineering specifications, equipment, and design standards often led to plants and equipment designed or built in Europe falling short of American engineering standards, resulting in costly delays due to redesign or rebuild.

After numerous attempts with American-based integrators, the customer’s projects struggled to take off, burdened with costly delays and setbacks. However, a new dawn broke when the customer partnered with Pigler Automation. This was the turning point that led to a successful and creative solution.
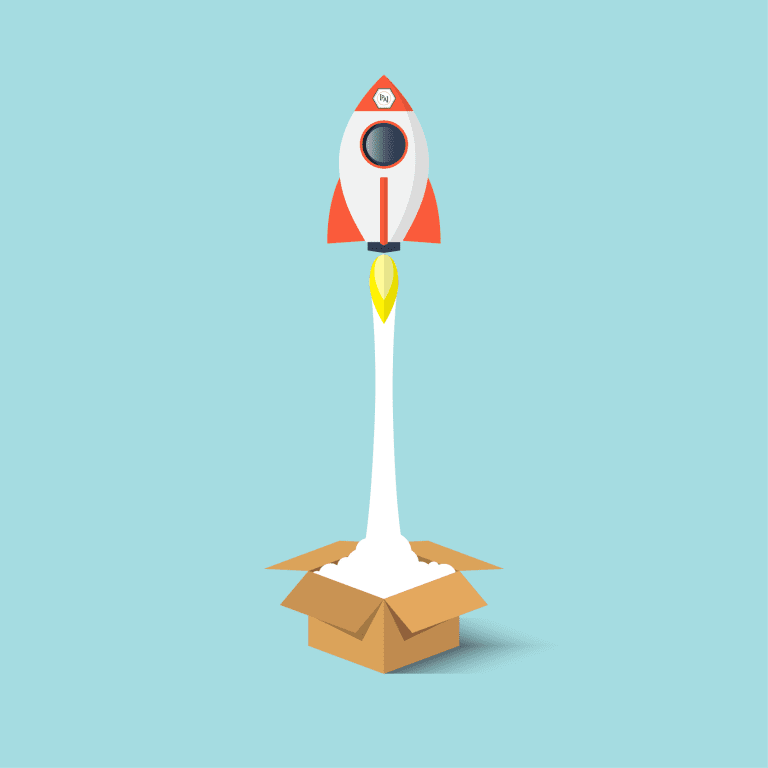
Complex Challenge, Outside the Box Thinking
Through close collaboration with the customer, we gained a profound understanding of their challenges in building or modernizing plants in the United States. We then devised a truly innovative strategy to address our customers’ distinct project requirements, underscoring our dedication to finding novel solutions rather than rehashing the same unsuccessful approaches used by other integrators.
One of the biggest issues we identified was the lack of a unified controls strategy and documentation, which contributed to a disconnect between the customer’s office in Germany and the project work in the United States. We felt the customer would be better served if they had access to Pigler Automation’s expertise throughout all project stages, so we developed a plan to embed a Pigler Automation engineer with the team at the customer’s Germany location. We believed that we could break down barriers that impeded success by fusing our knowledge and experience with the customer’s existing engineering team. This would allow the customer’s in-house team to develop their project specifications under the guidance of a US engineering expert who can ensure that all components will meet US engineering standards and specifications.
When we initially proposed our concept to the customer, it was met with disbelief as it was an unexplored territory for integrators. However, as we outlined our plan and demonstrated our willingness to deploy one of our team members to Germany to better integrate with their team, the customer’s skepticism transformed into enthusiasm. Including one of Pigler Automation’s engineers in their team meant they could tap into our extensive knowledge and experience without the time and expense of hiring or sponsoring an engineer from the United States. In addition to the engineer we relocated to Germany, we were committed to local hiring and expanding our team in the country, further enhancing our partnership.
Customer First Solution
Our first step in building our new and enhanced relationship was to help develop and refine a unified controls strategy that could be applied to every plant throughout the customer’s global footprint. The strategy would include building a comprehensive library customized to include specific functionality, such as PID controllers and digital or analog monitoring with alarm functionality that can be used to build Control Module Templets (CMTs) for commonly used charts. This would help with operational continuity, ensure that the same standards are applied to existing and new plants, and allow for efficient updates no matter the location.
Along with building a unified controls strategy, we identified that the customer would greatly benefit from developing and revising documentation related to current standards, including I/O lists, alarm lists, system architecture diagrams, and panel drawings. Creating this standard documentation would not only help increase efficiency with project execution but also offer a clear and reliable framework for future projects. Eliminating redundant documentation or consolidating multiple documents with similar information would also reduce confusion due to overlapping or conflicting information and help ease document control.
While standardization across all the customer’s plants and facilities is crucial, we also understand that we could not use a one-size-fits-all approach as different sites may require different solutions based on production load, location, ambient condition, etc. This is why we developed standards that could be deployed unilaterally while giving each location the discretion to modify parameters based on their unique requirements, ensuring adaptability and efficiency.
Embedding our Engineer with the customer’s in-house team in Germany also allowed us to leverage our relationships with US panel-building companies. This is especially beneficial for customer plants based in the United States as it would help to ensure the industrial control panels meet UL 508A compliance requirements while still adhering to the customer’s standards and specifications. This would ensure the successful transfer of projects from Germany to the United States and help establish an open line of dialogue between the German and American teams.
This unique, customer-first solution will help the customer’s current and future projects reach high-level goals more consistently by providing engineering and operational personnel with explicit guidelines to reference and reduce variance from plant to plant. Our partnership supports the customer’s goals of strengthening its position in the United States industrial gas market and positively impacting project success.
Pigler Automation’s Eye on the Future
Our unique approach to our customer’s complex challenge influenced the development of EXPERTFUSION™, our hybrid project solution that leverages the strength of Pigler Automation’s team and expertise combined with the customer’s in-house team to tackle complex issues and helps ensure the continued success of the customer’s operations.
Working with our customer’s German team, Pigler Automation has taken a step towards future collaboration within the German and European markets. Relocating and embedding our engineers with the German team will allow us to work closely with our customers, identify new opportunities to expand, and build lasting relationships with our people and companies that improve the world.
Learn more about how EXPERTFUSION™ can help you bridge the Industrial Control System Gaps