Unplanned downtime costs industrial manufacturers an estimated $20 billion every year—and a significant portion of it is avoidable.
Better testing, validation, and control logic checks can catch many issues that cause delays, shutdowns, and unsafe conditions before a system goes live. That’s where simulation comes in.
In this post, Senior Engineer Teddy Klovstad shares real-world examples of how simulation has helped us catch problems early, streamline development, and give clients confidence in their systems before the first valve turns.
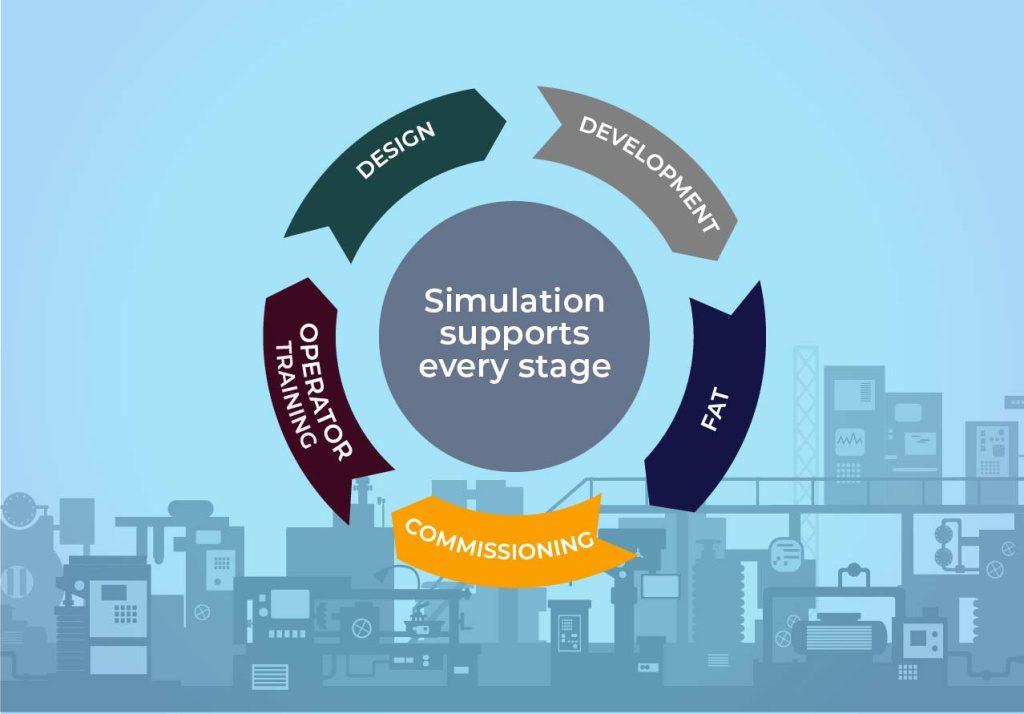
Catching Issues Before They Become Problems
According to Teddy, one of the biggest advantages of simulation is the ability to catch mistakes early—long before a technician stands on-site in front of a live system.
“Simulation lets us safely test alarms, interlocks, and sequences,” Teddy explains. “We can even introduce faults to see how the logic reacts. That way, we know things will behave correctly in the real world.”
In one project, Teddy built out a complex sequence and assumed everything would shut down safely if stopped mid-run. But when he simulated that scenario, he noticed a valve failed to close—a minor oversight that could have had real-world consequences. The fix was simple and safe because the issue was caught in the simulation.
Get It Right the First Time—Then Scale
Simulation also streamlines development. Instead of building dozens of control loops and hoping they’re configured correctly, Teddy will simulate the first few, validate the logic and client preferences, and then scale from there.
“If you build 50 loops and then realize you missed a key setting, it means rework,” he explained. “Simulation lets us get it right from the start.”
This approach is especially valuable during FAT (Factory Acceptance Testing), where clients can see and approve system behavior before we go to site. The result? Fewer revisions, faster commissioning, and systems that work the way they should—the first time.
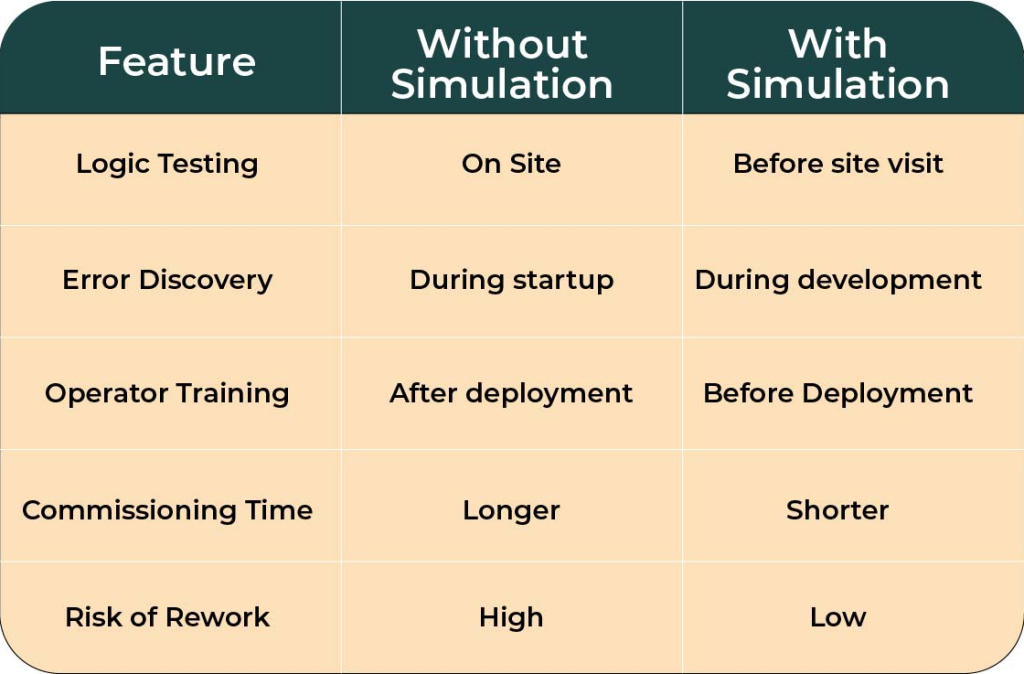
Understand Legacy Code Without the Guesswork
Simulation isn’t just for new builds. It’s also a critical tool when working with existing installations—especially systems without documentation or standardized logic. By recreating these environments in simulation, we can see how the logic behaves and identify where updates are needed before making changes.
With simulation, we can:
- Catch logic errors before they hit production
- Validate alarm and interlock sequences safely
- Train operators in a risk-free environment
- Evaluate legacy systems without complete documentation
For operators, simulation provides a safe, interactive environment to train on HMI screens and alarm conditions before the plant goes live.
“It helps build confidence on both sides,” Teddy noted. “Operators know what to expect, and clients know their team is ready.”
Looking Ahead: Digital Twins and AI Testing
We see huge potential in expanding simulation into digital twin technologies and AI-assisted testing. These tools could make simulation even more powerful—automating test case generation, modeling entire facilities, and speeding up development across industries.
Until then, our approach is simple: test, validate, and de-risk every system before it hits the floor. Simulation makes it possible, and the lessons we’ve learned prove just how much it pays off.
Ready to take the guesswork out of your next upgrade?
Talk to an engineer about how simulation can save time and reduce risk.